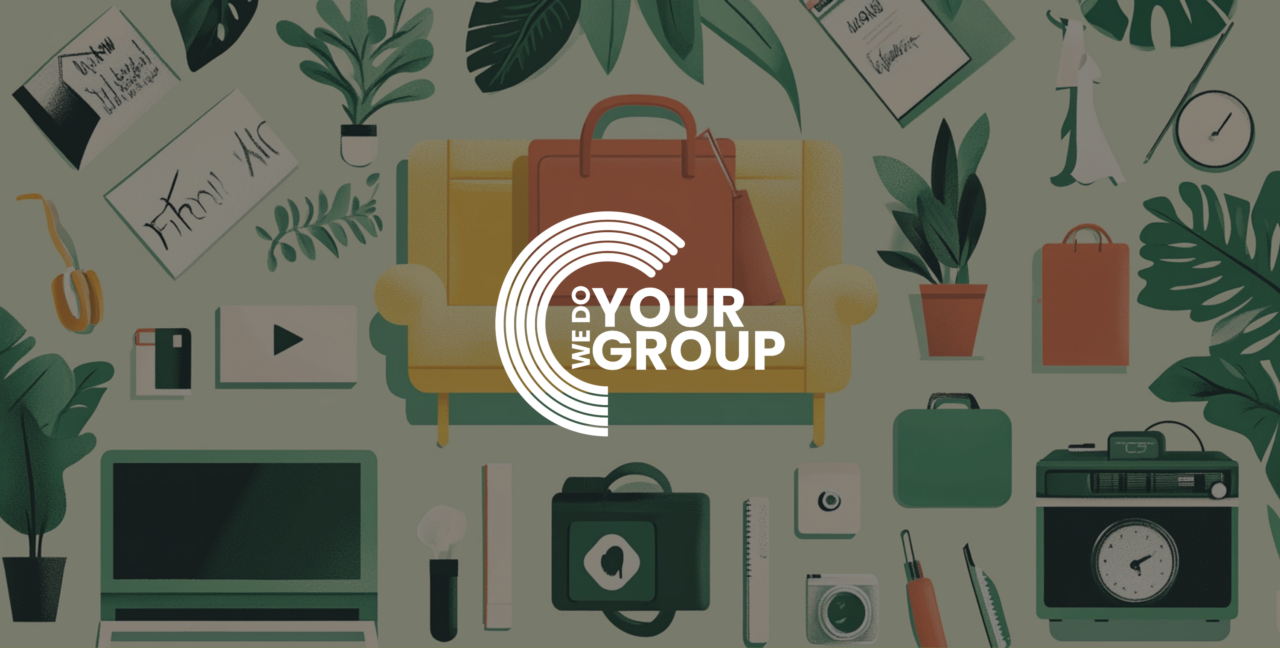
The introduction of additive manufacturing, specifically metal printing using stainless steel wire, into the cosmos marks a groundbreaking milestone in space exploration. This advanced technology, pioneered by Airbus, is ushering in a new era of self-sufficiency for astronauts in the space environment. It enables the production of strong, durable tools directly aboard spacecraft and the International Space Station. The implications of this innovation are profound, conserving crucial space and weight during spaceflights. Moreover, it heralds a shift towards sustainable, on-demand manufacturing in space. The vision of a moon base constructed from lunar materials using this 3D printer is nearing reality, promising endless possibilities for extended human presence and construction beyond our planet.
The deployment of the state-of-the-art 3D printer on the International Space Station, a testament to the ingenuity of European space energy, is revolutionising space exploration technologies. This cutting-edge technology allows astronauts to craft tools and components on-demand, mitigating the impact of space environment affects. By eliminating the need to wait for supplies from Earth, crews can promptly undertake repairs and improvements, boosting their autonomy in the sealed metal box of low-Earth orbit. The printing process enhances efficiency, safety, and well-being of the ISS inhabitants, making it a game-changer in space exploration.
The environmental impact of the pioneering metal 3D printer goes beyond the confines of the International Space Station. By localising tool-production in space and utilizing printers’ internal oxygen atmosphere, we significantly reduce the carbon footprint associated with transporting materials from Earth. This on-orbit manufacturing process, with the use of advanced materials and expertise from ESA materials engineers, allows for leaner, more eco-friendly space missions. Furthermore, it paves the way for utilising lunar or Martian resources to build bases, minimising reliance on Earth’s resources. The inclusion of liquid metals’ surface tension adds to the implications of in-space manufacturing, contributing not only to a sustainable future in space exploration but also promoting the conservation of our home planet’s vital resources.
As humanity sets its sights on the moon for future exploration and habitation, the metal 3D printer emerges as a cornerstone technology demonstration project. It holds the promise of making in-space manufacturing a reality, where the print process begins using in-situ resources, thereby drastically reducing the need to launch building materials from Earth. Envisage future lunar astronauts using this printer to create habitats, life-supporting structures, or even sinter lunar dust into concrete-like materials with a melting point specifically optimised for lunar conditions. This innovative leap is not just a boon for space travellers but also a giant stride towards realising the dream of a self-sustaining extraterrestrial presence, thereby redefining our capabilities for long-term space expeditions.
Employing a metal 3D printer in space is a bold innovation that has the potential to revolutionise lunar infrastructure development. With the capability to leverage lunar materials, this technology enables sustainable and resource-efficient in-situ production, paving the way for constructing a moon base. Imagine an ESA materials engineer using the moon’s regolith to forge not only structures, habitats, and tools but also more complex metallic structures, reducing cargo weight and costs from Earth-bound supply missions. This process eliminates the need to transport hefty materials across space, thus lowering barriers to establishing permanent human settlements on the moon and potentially sparking a new era of space colonisation, including the construction of space stations.
In the pursuit of establishing a functional 3D printer in the unique conditions of space, the industrial team led by paramount importance is placed on safety and operability in a micro-gravity environment. Overcoming these primary challenges entails meticulous engineering to ensure the printer can cope with the absence of gravity, which affects both the handling of raw materials, including metal alloys, and the solidification processes inherent to metal 3D printing. Secure containment systems are necessary to prevent the escape of any particulate matter, which could pose a serious risk to both the health of astronauts and the sensitive equipment aboard. In addition, consistent quality assurance protocols are crucial to certify the structural integrity and reliability of each printed component, especially complex components, which must withstand the rigours of space and contribute positively to the sustainability and advancement of our extraterrestrial endeavours.
The implementation of metal 3D printing technology extends its potential benefits to addressing global environmental concerns, most notably climate change. The lean production methods offered by this technology minimise waste and can reduce the energy consumption associated with traditional manufacturing processes. With the capacity to create intricate and lightweight structures that demand fewer resources, 3D printing stands at the forefront of developing sustainable materials and energy-efficient solutions. By transitioning towards a circular economy, where materials are reused and products are made closer to their point of use, such as in space, this technology could well be a game changer in mitigating Earth’s growing climate crisis, demonstrating that the applications of 3D printing hold the promise of not just altering how we conduct space exploration, but also how we safeguard our planet’s future.
The 3D metal printer in space is revolutionising operations in the vacuum of space. Not only that, but its potential applications on Earth are equally compelling. With printers’ internal oxygen atmosphere, this versatile technology opens up innovative avenues in various industries. Healthcare benefits from customised medical implants, while automotive and aerospace can produce complex parts with unprecedented speed and efficiency. The principles of in-situ resource utilisation derived from space manufacturing can be mirrored on Earth, resulting in more sustainable industrial practices. By reducing the need for extensive logistics networks and decreasing manufacturing waste, the ripple effects of space technologies, such as the 3D printer, promise to catalyse advancements in sustainability and production across a multitude of terrestrial domains. Furthermore, these printers can perform mechanical strength tests to ensure optimal performance.
Incorporating additive manufacturing, particularly metal 3D printing, within UK industries presents a significant opportunity for conserving essential resources like water and protecting wildlife. This technology, which refines manufacturing processes to be more precise and efficient, not only reduces waste and excess water usage associated with conventional production but also takes advantage of the unique properties of liquid metal’s surface tension in a microgravity environment. By adopting these innovations, UK companies align with environmental regulations and contribute to the preservation of natural habitats by mitigating industrial water pollution. This partnership between advanced technology, sustainability initiatives, and the expertise of ESA technical officers provides an impetus for businesses to operate more responsibly, offering a blueprint for industry-wide adoption that nurtures biodiversity and promotes water conservation efforts on a local and national scale.