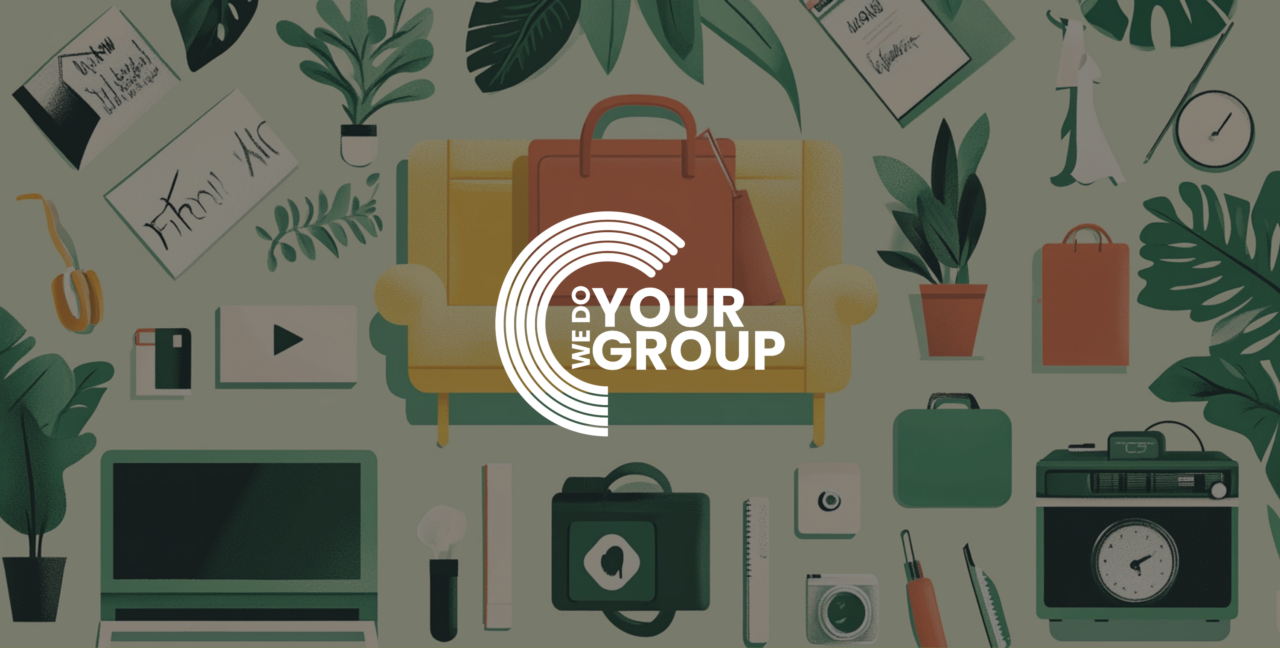
Maine University’s Composites Center has made a revolutionary advancement in manufacturing with the launch of the Factory of the Future 1.0 (FoF 1.0), currently the largest 3D printer in the world. This immense printer, quadrupling the size of its predecessors, marks a significant shift towards advanced production processes. Beyond its impressive size, the FoF 1.0 is distinguished by its ability to seamlessly integrate various manufacturing techniques, including additive and subtractive manufacturing, continuous tape layup, and the use of robotic arms, making it a leader in technological innovation. This printer’s capacity to fabricate large-scale objects up to 96 feet in length not only escalates production capabilities but also facilitates advancements in sectors such as construction, national defense, and the creation of eco-friendly materials. By potentially reducing greenhouse gas emissions compared to traditional methods, the FoF 1.0 could play a crucial role in addressing global challenges like affordable housing and environmental sustainability. Maine University’s introduction of the FoF 1.0 underscores its dedication to driving the future of industry through reduced environmental impact and innovative production techniques.
The Factory of the Future 1.0 (FoF 1.0), unveiled by the University of Maine, marks a groundbreaking advancement in manufacturing technology, setting a world record with its combination of size, speed, and flexibility. This advanced system excels in producing objects up to 96 feet long, achieving a production rate of 500 pounds per hour, and has the capacity to handle a vast cubic meter volume, making it ideal for printing large-scale objects like ship propellers. FoF 1.0’s production process is innovative, incorporating both additive and subtractive manufacturing, continuous tape layup, and precision tasks executed by robotic arms, enabling the creation of advanced structures with unparalleled efficiency. Its ability to produce cheap houses and eco-friendly materials demonstrates its enormous potential to transform various industries, highlighting FoF 1.0 as a key solution to some of the most pressing global challenges.
The Factory of the Future 1.0 (FoF 1.0), designed by Maine University, represents a next-generation leap in manufacturing, capable of printing objects on a large scale. This cutting-edge 3D printer introduces eco-friendly production techniques on a scale never seen before, using biobased feedstocks from wood residues. This method promises to drastically cut the carbon footprint associated with traditional manufacturing over the next six years. Moreover, its capability extends beyond environmental benefits, offering a significant asset for national security. The Army Corps of Engineers could leverage FoF 1.0 to print robust infrastructure or quickly deploy shelters in crisis zones, showcasing its broad applicability from large scale 3D printing to critical national defense projects. FoF 1.0 is poised to transform manufacturing and address societal challenges, marking a pivotal advancement in technology’s ability to print objects and meet diverse needs.
Facing an urgent demand for around 80,000 additional homes by 2030, Maine is at a pivotal point in tackling its housing crisis. The University of Maine’s Factory of the Future 1.0 (FoF 1.0) project stands out as a promising solution. With its cutting-edge additive manufacturing capabilities, including the use of 3D printers, FoF 1.0 is poised to transform the market for affordable housing. This project leverages 3D printing and eco-friendly materials to streamline the production of durable, cost-effective homes on a large scale. By adopting this innovative approach, Maine can significantly address its housing shortage, benefiting thousands of residents and establishing a model for future housing solutions globally.
The launch of the Factory of the Future 1.0 (FoF 1.0) at the University of Maine marks a significant departure from traditional manufacturing methods, showcasing a new era in the use of composite materials. This groundbreaking initiative, housed in the university’s Composites Center, displays a fusion of advanced manufacturing techniques. The FoF 1.0, a monumental 3D printer, moves beyond conventional boundaries by incorporating a range of capabilities, from additive and subtractive manufacturing to the cutting-edge application of continuous tape layup and robotic arm technology. Distinguished by its capacity to manufacture large-scale objects and its innovative employment of biobased feedstocks—derived from wood residues—the FoF 1.0 leads the way in developing sustainable solutions. These eco-friendly materials are not only a nod to sustainability but also signal advancements in composite material technology. With machines that enable the production of items up to 96 feet in length swiftly, the FoF 1.0 epitomizes the integration of speed, size, sustainability, and advanced material application. It positions the University of Maine at the forefront of the global movement toward innovative manufacturing solutions, underscoring the department’s commitment to service and excellence in developing future-ready manufacturing technologies.
The Department of Engineering at Maine University has created the Factory of the Future 1.0 (FoF 1.0), a world record-setting initiative in the realm of green engineering and sustainable manufacturing. This innovative project employs 3D printing technology, also known as additive manufacturing, on a large scale to print objects using biobased feedstocks from wood residues. FoF 1.0 represents a significant advancement in the use of eco-friendly materials in manufacturing processes, creating a sustainable alternative to traditional methods. By leveraging additive manufacturing for large-scale creation of objects, FoF 1.0 not only reduces the carbon footprint associated with production but also demonstrates how sustainable practices can align with technological progress and industrial efficiency. This groundbreaking approach establishes a new benchmark for manufacturing in various sectors, including construction and national defence, proving the viability of integrating green technologies to tackle pressing environmental challenges.
Maine University’s engineers have created the Factory of the Future 1.0 (FoF 1.0), a trailblazer in energy-efficient building techniques, leveraging the advantages of additive manufacturing. This innovative approach utilizes biobased components derived from wood residues, making it not only sustainable but also cost-effective. Particularly beneficial in the creation of cheap houses, FoF 1.0 can also be applied to commercial and industrial buildings, offering a green alternative by using less plastic and other non-renewable resources. Its capacity to rapidly produce large-scale objects, such as boats, with minimal waste underlines its potential to revolutionize the construction sector. This places Maine University at the forefront of sustainable construction and green engineering, showcasing their commitment to reducing the environmental footprint of building processes.
The launch of the Green Engineering and Materials Factory represents a significant leap towards environmental sustainability, integrating the advanced capabilities of the Factory of the Future 1.0 (FoF 1.0) with a focus on 3D printed solutions. This initiative, led by Maine University, is pioneering the use of eco-friendly practices in manufacturing and construction, including the creation of cheap houses and other printing objects. The FoF 1.0 technology, notable for its employment of biobased feedstocks from wood residues, enables the factory to utilize 3D printers for producing materials that transform traditional building methods. This innovative approach not only minimizes the carbon footprint of these sectors but also demonstrates the practical advantages of adopting sustainable methods. By leveraging 3D printing technology and composite materials, the factory aims to revolutionize how we think about manufacturing and construction, making it a symbol of hope for a greener planet. This underscores Maine University’s dedication to leading the way in green engineering solutions, including the production of affordable housing through 3D printing.
The Factory of the Future 1.0 (FoF 1.0), developed by Maine University, highlights the innovative use of technology to tackle global challenges. Central to its mission is enhancing the manufacturing and construction industries by introducing advanced, sustainable practices. These include additive manufacturing and large-scale 3D printing using biobased materials, significantly reducing environmental impact. FoF 1.0 pioneers in transforming production and building processes, offering scalable, affordable solutions for things like a cheap house, combating environmental degradation, and meeting the demand for sustainable infrastructure. This initiative reflects Maine University’s dedication to using cutting-edge technology for a sustainable, equitable future.